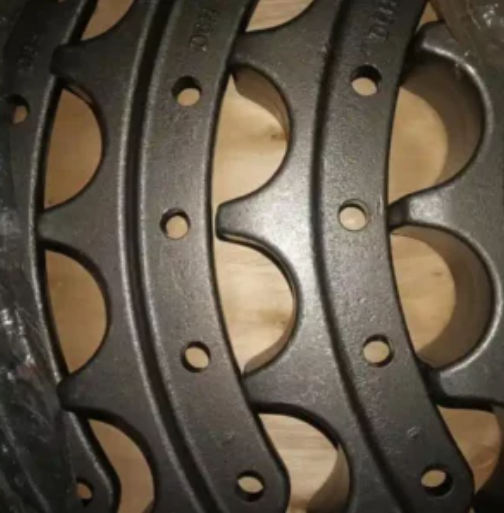
Understanding the difference between the excavator drive sprockets and driven sprockets is crucial for machinery maintenance. These components play vital roles in the operation of heavy machinery like excavators.
Excavator Drive Sprockets
Excavator drive sprockets are essential for transmitting power. Located on the excavator’s motor, they engage with the track chain to propel the machine. Their primary function is converting rotational power from the engine into linear motion.
Driven Sprockets
Driven sprockets, also known as rear or final sprockets, receive power from the drive sprockets. They are part of the track system that ensures smooth movement. Driven sprockets help in maintaining the tension and alignment of the track.
Key Differences
Function
Excavator drive sprockets provide power and initiate motion. Driven sprockets receive this power and help in movement. Both work together to move the excavator efficiently.
Location
Drive sprockets are connected to the engine. They are typically located at the front of the track system. Driven sprockets are positioned at the rear, helping in track tension and alignment.
Design
Drive sprockets have teeth designed to engage with the track links. Driven sprockets, while similar, are designed to follow the track’s movement without providing direct power.
Material and Durability
Applications in Excavators
Both excavator drive sprockets and driven sprockets are made from durable materials. This ensures they can withstand harsh conditions and heavy loads. Regular maintenance prolongs their lifespan.
The interplay between drive and driven sprockets is crucial for excavator operation. The drive sprocket’s engagement with the track chain provides the necessary power. This enables the excavator to move forward or backward.
Importance of Maintenance
Regular inspection and maintenance of both the excavator sprocket and driven sprocket are vital. Worn-out sprockets can lead to inefficient operation and increased wear on the track system. Replacing them when needed ensures smooth operation.
Common Issues and Solutions
Worn Teeth
Worn teeth on either the sprocket excavator or driven sprocket can cause slippage and inefficient power transmission. Regular inspection and timely replacement prevent these issues.
Misalignment
Misalignment of sprockets can lead to uneven wear and track derailment. Ensuring proper alignment during installation and maintenance is crucial.
Lubrication
Proper lubrication of the track system, including the excavator sprocket, reduces friction and wear. Regular lubrication extends the lifespan of these components.
Choosing the Right Sprocket
When selecting excavator drive sprockets, consider the following:
- Compatibility: Ensure the sprocket fits your specific excavator model.
- Material: Choose sprockets made from high-quality, durable materials.
- Brand: Opt for reputable brands known for their reliability and quality.
Excavator Sprocket Price
The price of an excavator sprocket varies based on quality, brand, and compatibility. High-quality sprockets from reputable brands tend to be more expensive. However, investing in quality ensures durability and better performance.
Conclusion
Understanding the differences between drive and driven sprockets is essential for maintaining your excavator. Excavator drive sprockets provide the necessary power for movement. Driven sprockets receive this power and help maintain track tension. Regular maintenance of both components ensures efficient operation. Choose high-quality sprockets to enhance your excavator’s performance and lifespan.
What is the Difference Between Drive Sprocket and Driven Sprocket?
Introduction
Understanding the difference between the excavator drive sprockets and driven sprockets is crucial for machinery maintenance. These components play vital roles in the operation of heavy machinery like excavators.
Excavator Drive Sprockets
Excavator drive sprockets are essential for transmitting power. Located on the excavator’s motor, they engage with the track chain to propel the machine. Their primary function is converting rotational power from the engine into linear motion.
Driven Sprockets
Driven sprockets, also known as rear or final sprockets, receive power from the drive sprockets. They are part of the track system that ensures smooth movement. Driven sprockets help in maintaining the tension and alignment of the track.
Key Differences
Function
Excavator drive sprockets provide power and initiate motion. Driven sprockets receive this power and help in movement. Both work together to move the excavator efficiently.
Location
Drive sprockets are connected to the engine. They are typically located at the front of the track system. Driven sprockets are positioned at the rear, helping in track tension and alignment.
Design
Drive sprockets have teeth designed to engage with the track links. Driven sprockets, while similar, are designed to follow the track’s movement without providing direct power.
Material and Durability
Both excavator drive sprockets and driven sprockets are made from durable materials. This ensures they can withstand harsh conditions and heavy loads. Regular maintenance prolongs their lifespan.
Applications in Excavators
The interplay between drive and driven sprockets is crucial for excavator operation. The drive sprocket’s engagement with the track chain provides the necessary power. This enables the excavator to move forward or backward.
Importance of Maintenance
Common Issues and Solutions
Regular inspection and maintenance of both the excavator sprocket and driven sprocket are vital. Worn-out sprockets can lead to inefficient operation and increased wear on the track system. Replacing them when needed ensures smooth operation.
Worn Teeth
Worn teeth on either the sprocket excavator or driven sprocket can cause slippage and inefficient power transmission. Regular inspection and timely replacement prevent these issues.
Misalignment
Misalignment of sprockets can lead to uneven wear and track derailment. Ensuring proper alignment during installation and maintenance is crucial.
Lubrication
Proper lubrication of the track system, including the excavator sprocket, reduces friction and wear. Regular lubrication extends the lifespan of these components.
Choosing the Right Sprocket
When selecting excavator drive sprockets, consider the following:
- Compatibility: Ensure the sprocket fits your specific excavator model.
- Material: Choose sprockets made from high-quality, durable materials.
- Brand: Opt for reputable brands known for their reliability and quality.
Excavator Sprocket Price
The price of an excavator sprocket varies based on quality, brand, and compatibility. High-quality sprockets from reputable brands tend to be more expensive. However, investing in quality ensures durability and better performance.
Conclusion
Understanding the differences between drive and driven sprockets is essential for maintaining your excavator. Excavator drive sprockets provide the necessary power for movement. Driven sprockets receive this power and help maintain track tension. Regular maintenance of both components ensures efficient operation. Choose high-quality sprockets to enhance your excavator’s performance and lifespan.