When moving an excavator across a site, positioning the excavator sprocket rim correctly is crucial. Proper positioning ensures safety and efficiency. Understanding where the drive sprockets should be can prevent damage and improve performance.
The drive sprockets’ position affects the excavator’s balance and traction. Proper placement reduces wear and tear on the machine. It also enhances operator control and safety during movement.
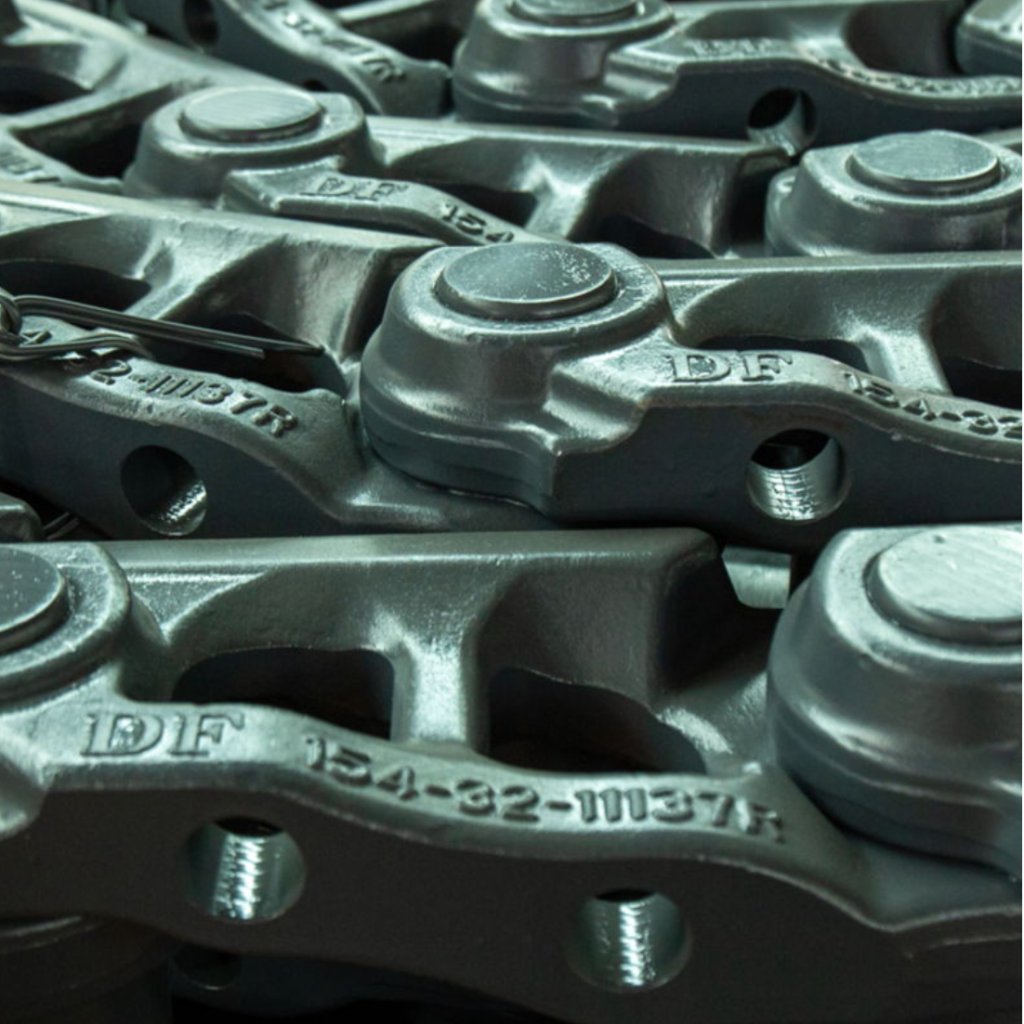
Front vs. Rear Drive Sprockets
Front Drive Sprockets
Positioning the drive sprockets at the front is common during travel. This setup offers better control and stability. It also reduces the risk of track derailment on uneven terrain.
Rear Drive Sprockets
In some cases, the drive sprockets are positioned at the rear. This configuration provides more power for challenging terrains. However, it may reduce control on smooth surfaces.
Factors Influencing Sprocket Position
Terrain
Assess the terrain before moving the excavator. On rough or uneven ground, front drive sprockets offer better stability. For steep inclines, rear drive sprockets provide more traction.
Load Balance
Distribute the excavator’s load evenly. Proper load balance reduces stress on the excavator sprocket rim. This prevents premature wear and potential damage.
Speed and Maneuverability
Front drive sprockets allow for better maneuverability at higher speeds. This positioning helps navigate tight spaces and obstacles efficiently.
Safety Considerations
Operator Visibility
Ensure the operator has a clear view. Positioning the drive sprockets at the front enhances visibility. This reduces the risk of accidents and improves site safety.
Track Tension
Maintain proper track tension regardless of sprocket position. Loose tracks can derail, causing delays and potential damage.
Manufacturer Recommendations
Follow guidelines from excavator sprocket manufacturers. They provide specific recommendations based on machine design and intended use. Adhering to these guidelines ensures optimal performance and longevity.
Common Mistakes and Solutions
Incorrect Sprocket Position
Placing drive sprockets incorrectly can lead to control issues. Always assess the site conditions and adjust accordingly.
Ignoring Terrain
Ignoring terrain type can cause unnecessary wear. Adapt the sprocket position based on the specific ground conditions.
Overloading
Avoid overloading the excavator. Excess weight strains the excavator sprocket rim and other components. Balance the load to maintain efficiency and safety.
Maintenance Tips for Sprocket Longevity
Regular Inspections
Inspect the excavator sprocket rim regularly. Look for signs of wear and replace worn parts promptly.
Lubrication
Proper lubrication reduces friction and wear. Lubricate the sprockets and track system as recommended by excavator sprocket manufacturers.
Alignment
Ensure sprockets are aligned correctly. Misalignment can cause uneven wear and potential track derailment.
Sourcing Quality Sprockets
Excavator Sprocket Manufacturers
Choose reputable excavator sprocket manufacturers. Quality manufacturers provide durable and reliable sprockets.
Excavator Sprocket Quotes
Obtain multiple excavator sprocket quotes. Compare prices and features to find the best value.
Compatibility
Ensure the sprockets are compatible with your excavator model. Using the correct parts prevents damage and ensures optimal performance.
Conclusion
Properly positioning the excavator sprocket rim when traveling across a site is vital for safety and efficiency. Consider terrain, load balance, and manufacturer guidelines. Follow maintenance tips to extend sprocket lifespan. Sourcing quality sprockets from reputable excavator sprocket manufacturers ensures reliability and durability. Remember to compare excavator sprocket quotes to get the best value. Proper sprocket positioning and maintenance will enhance your excavator’s performance and longevity.